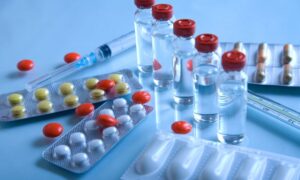
Pharmaceutical manufacturing involves a vast array of chemicals, from solvents and powders to acids and bases. These substances can pose significant health risks if not handled properly with an industrial exhaust system.
By effectively capturing and removing airborne contaminants, these systems create a safe and controlled environment for pharmaceutical production. This not only protects workers from harmful exposures but also ensures product quality and consistency.
At Eldridge, we understand the unique challenges of clean environment ventilation. Our industrial exhaust systems are designed to meet the stringent demands of this industry, providing reliable protection against hazardous chemicals and ensuring compliance with regulatory standards. Contact us now to learn how we can help you achieve optimal safety and efficiency in your pharmaceutical processing facility.
Types of Pharmaceutical Production Processes
Each stage of production has a unique set of challenges and potential hazards.
Active Pharmaceutical Ingredient (API) Manufacturing
This initial stage involves creating the active ingredient that gives a drug its therapeutic effect. API manufacturing can be divided into three primary methods:
- Synthesis: This method uses chemical reactions to combine different molecules and create new compounds.
- Extraction: This process involves isolating the active ingredient from natural sources like plants or animals.
- Fermentation: This biological process utilizes microorganisms like bacteria or yeast to produce the desired compound.
Each of these methods involves the use of various chemicals, including solvents, reactants, and byproducts, which can pose risks to workers’ health and the environment if not adequately controlled by industrial exhaust systems.
Formulation and Filling
Once the API is produced, it undergoes formulation, where it’s combined with inactive ingredients to enhance stability, improve taste, or facilitate drug delivery. This process often involves mixing powders, liquids, or both, which can generate dust, vapor, and aerosols. These airborne particles can be easily inhaled, potentially causing respiratory issues.
Packaging and Labeling
The final stage involves packaging the formulated drug and applying labels with essential information like dosage, warnings, and storage instructions.
Although it may not seem to be as overtly dangerous as other types of processes, this stage also carries potential hazards, mainly due to the use of printing inks and certain packaging materials, which may release volatile organic compounds (VOCs) into the air. Exposure to VOCs can cause a variety of health problems, ranging from eye, nose, and throat irritation to headaches, nausea, and damage to the liver, kidneys, and nervous system. Some VOCs are even suspected or known to cause cancer.
Common Chemicals Used in Pharmaceutical Production
Many of the substances used to create pharmaceuticals pose potential health and environmental hazards during processing. Understanding the specific chemicals used in your facility and their associated hazards is the first step towards designing an effective industrial exhaust system.
Solvents
Solvents like methanol, ethanol, acetone, and toluene are commonly used to dissolve, extract, or purify other substances during API synthesis and formulation. While essential, these solvents are often flammable and can be toxic if inhaled or absorbed through the skin. Long-term exposure to certain solvents can also damage the liver, kidneys, and nervous system.
Acids and Bases
Acids like hydrochloric acid and sulfuric acid, along with bases like sodium hydroxide, play crucial roles in various pharmaceutical processes, including pH adjustment and chemical reactions. These substances are highly corrosive and can cause severe burns upon contact with skin or eyes. Inhalation of their fumes can also irritate the respiratory system.
Powders and Dusts
API powders, excipients like lactose or starch, and other powdered materials are frequently used in pharmaceutical manufacturing. These substances can easily become airborne, creating dust clouds that pose inhalation hazards. Inhaling fine particles can lead to respiratory problems. Certain dusts may even be combustible, posing a risk of explosions in confined spaces.
In addition to these common chemicals, pharmaceutical production may involve other hazardous substances, depending on the specific drugs being manufactured. These could include highly potent active ingredients or other specialized chemicals with unique risks.
Types of Industrial Exhaust Systems for Pharmaceutical Production
Maintaining a clean and controlled environment in pharmaceutical production requires the right type of industrial exhaust system. General ventilation systems work by continuously introducing fresh air into the workspace and exhausting stale air. While they don’t capture contaminants directly, they help maintain overall air quality by diluting the concentration of airborne pollutants. General ventilation is essential for maintaining comfortable temperatures and humidity levels, which are crucial for both worker comfort and product stability.
Local Exhaust Ventilation (LEV) systems are designed to capture contaminants at their source, preventing them from dispersing into the workspace. These systems typically include hoods, enclosures, or capture arms placed near the point of generation of dust, fumes, or vapors. The captured air is then transported through ductwork to a filtration or treatment system before being safely exhausted outside the facility. LEV is particularly effective in controlling exposure to highly hazardous substances.
Some contaminants require specialized treatment beyond general ventilation or LEV. For instance, scrubbers are used to remove specific pollutants from exhaust air, such as acidic fumes or certain gases. HEPA filtration is highly effective at capturing fine particulate matter, including dusts and bioaerosols. Activated carbon filters are used to adsorb volatile organic compounds (VOCs), preventing their release into the environment.
Design Considerations for a Pharmaceutical Industrial Exhaust System
Determining the appropriate airflow rates and capture velocities is crucial for effectively capturing and removing contaminants. Airflow rates dictate the volume of air exhausted per unit of time, while capture velocities determine the speed at which air is drawn into the hood or enclosure.
These parameters are calculated based on factors like the type and quantity of contaminants, the size of the work area, and the distance between the source and the exhaust point. Properly calculated airflow rates and capture velocities ensure that contaminants are efficiently captured and prevented from escaping into the workspace.
The design and materials of the ductwork also has a direct impact on an industrial exhaust system’s performance and longevity. The ductwork must be sized appropriately to handle the required airflow without creating excessive pressure drops, which can strain the fan and reduce efficiency. The routing of the ductwork should be as direct as possible to minimize friction losses.
The choice of materials is equally important, as some chemicals can corrode certain metals. Stainless steel, PVC, or fiberglass-reinforced plastic (FRP) are common choices for pharmaceutical exhaust systems due to their chemical resistance and durability.
Effective Industrial Exhaust System for Pharmaceutical Production
The complex nature of pharmaceutical production requires a highly tailored approach to exhaust system design. At Eldridge, our expertise in industrial ventilation and exhaust systems allows us to design and implement solutions that meet the stringent requirements of cleanroom environments.
If you are looking to optimize your pharmaceutical production facility with a safe and efficient exhaust system, contact Eldridge today for an assessment and quote.