The air that workers breathe in an industrial workplace is crucial to their health, safety and productivity. Airborne contaminants impact air quality and pose a significant risk to workers. In this week’s blog, I’ll discuss ventilation strategies for controlling airborne contaminants to create a safer working environment.
Understanding Airborne Contaminants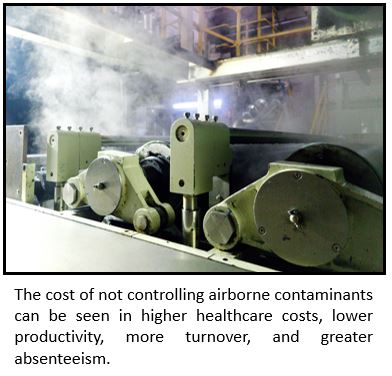
Before determining the best ventilation strategy, it’s crucial to understand the nature of contaminants. Airborne contaminants can be broadly categorized into:
- Particulates: These are tiny solid particles or liquid droplets suspended in the air. Examples include dust, pollen, soot, and mists. They can originate from various sources such as construction sites, vehicle exhausts, factories, and even natural processes like volcanic eruptions.
- Gases: These are substances that are airborne at room temperature. Examples include carbon dioxide (CO2), carbon monoxide (CO), ozone (O3), and volatile organic compounds (VOCs).
- Vapors: These are gaseous forms of substances that are typically in a solid or liquid state at room temperature. They arise from processes such as evaporation or sublimation. Examples include water vapor and solvent vapors.
- Fumes: These are small, fine, solid particles that are formed when a solid, such as metal, is rapidly vaporized and condenses as tiny particles. Welding, for instance, can produce fumes.
- Biological Agents: These include bacteria, viruses, fungi, and other microorganisms that might be suspended in the air, often attached to larger particulate matter.
Ventilation Strategies
Once the nature, size, density and amount of the airborne contaminant has been determined, the next step is to determine how it should be controlled. The two options are to either capture the airborne contaminant or dilute it. Here is a brief explanation of a local exhaust ventilation system used for capture and general ventilation system used for dilution.
Local Exhaust Ventilation (LEV)
LEV remains at the forefront of contamination control. It works on the principle of ‘capture at the source,’ ensuring contaminants are removed before they spread. These are the main components of an LEV:
- Capture Hood: Placed near or around the contaminant source to capture emissions.
- Ducts: Transport the captured contaminants away from the source.
- Air Cleaner: Filters and cleans the extracted air. This can include cyclones, scrubbers, electrostatic precipitators, or simple filter systems.
- Fan: Provides the necessary airflow.
- Exhaust Stack: Discharges the cleaned air to the outside, ensuring pollutants are released at a height where they can disperse without causing ground-level issues.
Here are the advantages and disadvantages of an LEV:
Advantages:
- High Efficiency: Captures contaminants directly at the source.
- Flexibility: Can be tailored for specific operations or machines.
- Reduced Worker Exposure: Limits the exposure of employees to harmful substances.
Disadvantages:
- Higher Cost: Typically more expensive than general dilution ventilation due to specialized equipment.
- Maintenance: Requires regular checks and maintenance to ensure capture hoods are positioned correctly and the system is working efficiently.
General Ventilation (GV)
This type of ventilation system dilutes contaminated air with clean, uncontaminated air, reducing the concentration of pollutants.
The main components of a GV are:
- Supply Fans: Introduce fresh air into the workspace.
- Exhaust Fans: Remove and discharge the polluted air.
- Vents and Louvers: Help control the direction and flow of air.
Here are the advantages and disadvantages of a GV:
Advantages:
- Simplicity: Generally simpler and more straightforward than LEV systems.
- Cost: Typically less expensive to install and maintain than LEV systems.
- Broad Coverage: Covers large areas and can be useful where contaminants are widespread rather than localized.
Disadvantages:
- Less Efficient: Doesn’t always reduce contaminant concentrations to safe levels, especially if the contaminant generation rate is high.
- Energy Costs: Continuously introducing fresh air can increase heating or cooling costs.
- Limitations: Not suitable for highly toxic or reactive contaminants.
Primary Applications
These are the applications where an LEV might be the best strategy:
- High-risk areas: These are where extremely toxic or hazardous substances are released.
- Localized sources: Operations like welding, grinding, or chemical mixing where contaminants have a specific point of release.
- Sensitive environments: Labs or research facilities where even minor contamination can skew results.
These are the applications where a GV might be the best strategy:
- Wide-spread, low-level contaminants: Where the contaminants are spread out and not intensely concentrated.
- Heat management: In environments like foundries where heat dissipation is as crucial as contaminant control.
- Odor control: In spaces like commercial kitchens or certain manufacturing units where the objective is to manage unpleasant odors.
Conclusion
A safe, healthy and productive environment should be the goal for workers in all industrial facilities. Achieving that goal requires controlling airborne so that workers aren’t at risk. At Eldridge, we have over 77 years of experience designing ventilation systems to control airborne contaminants. Call one of our ventilation experts and they will select and design the ventilation system to control your airborne contaminants.